Metro C: Stations and Shafts
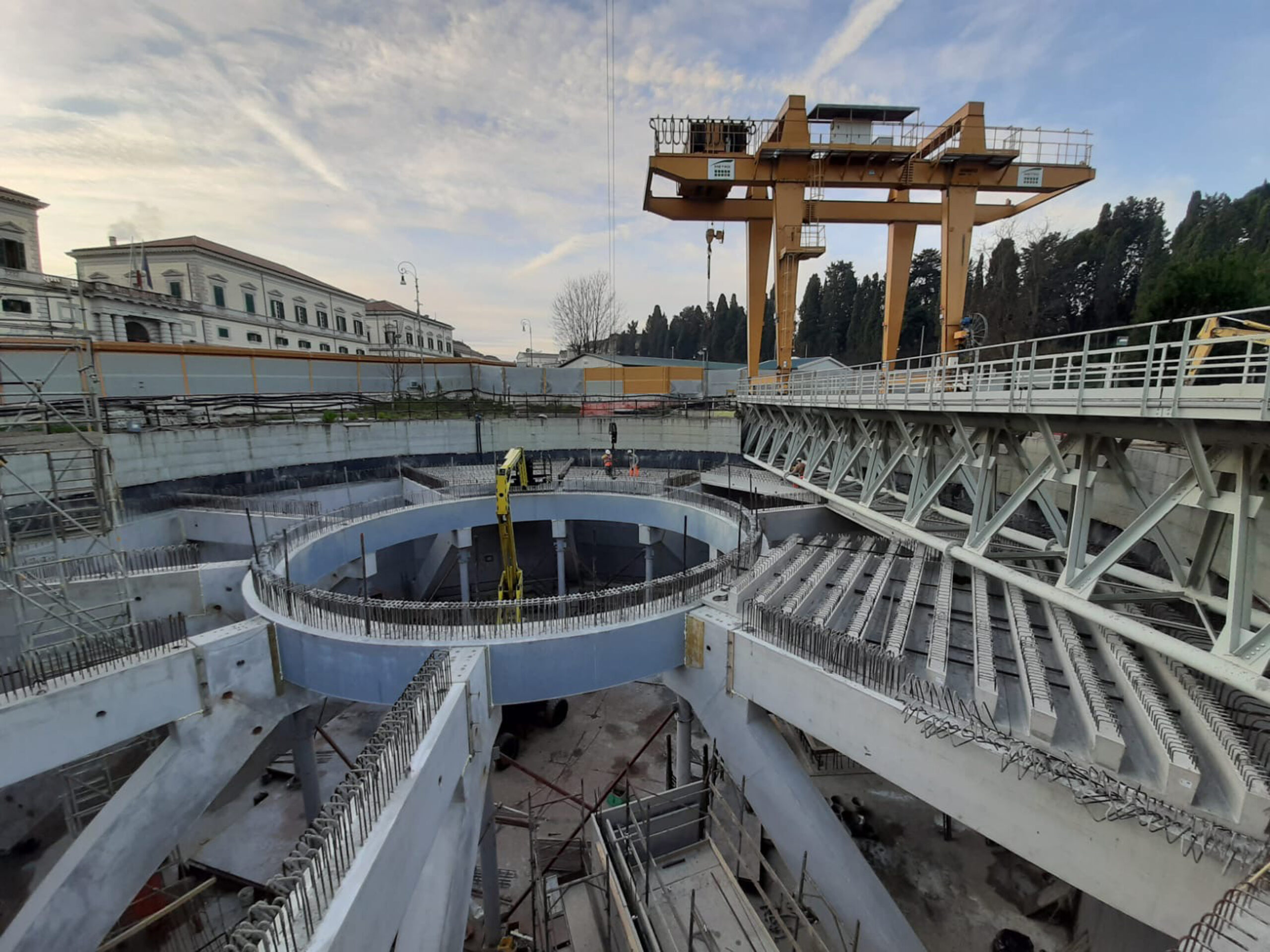
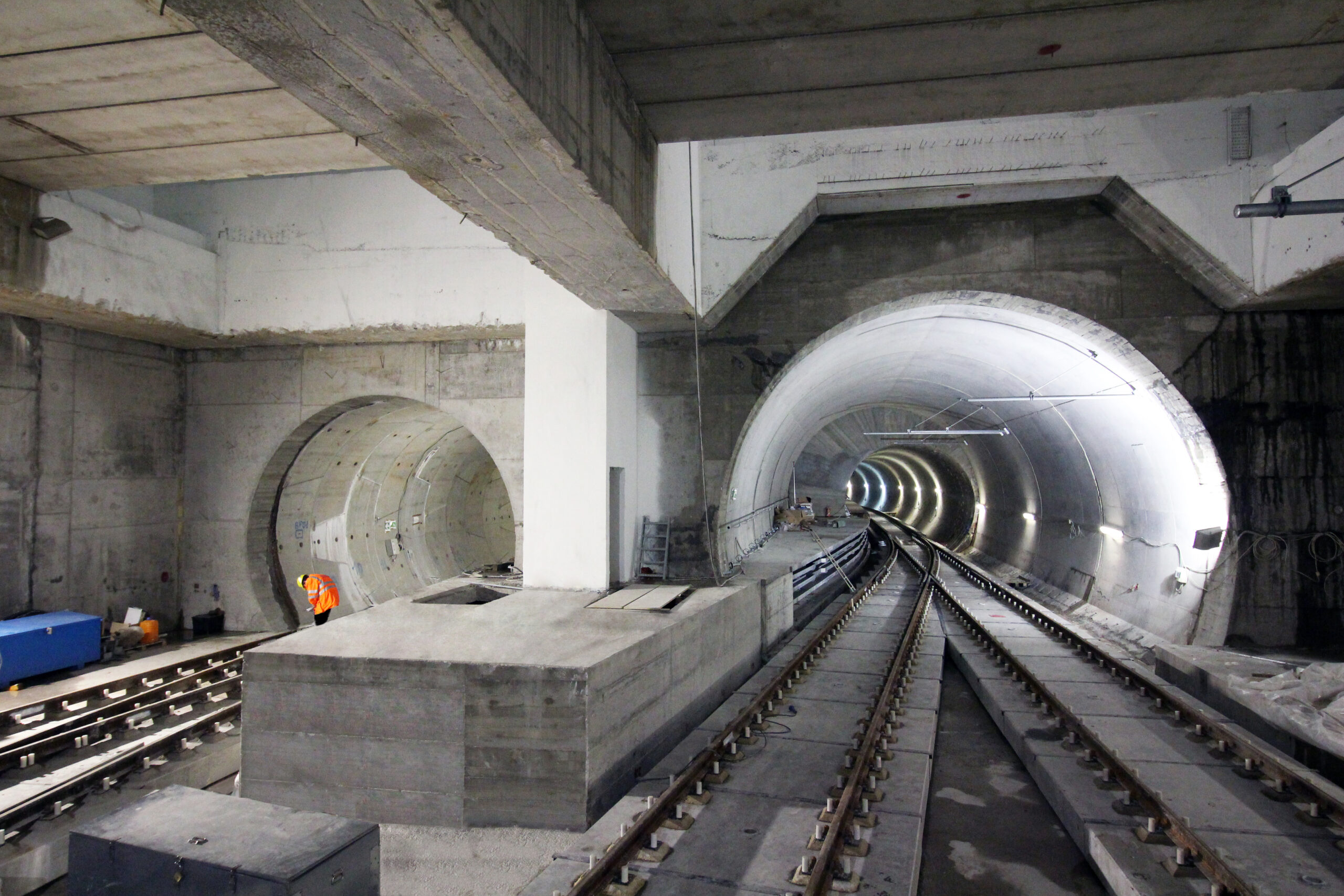
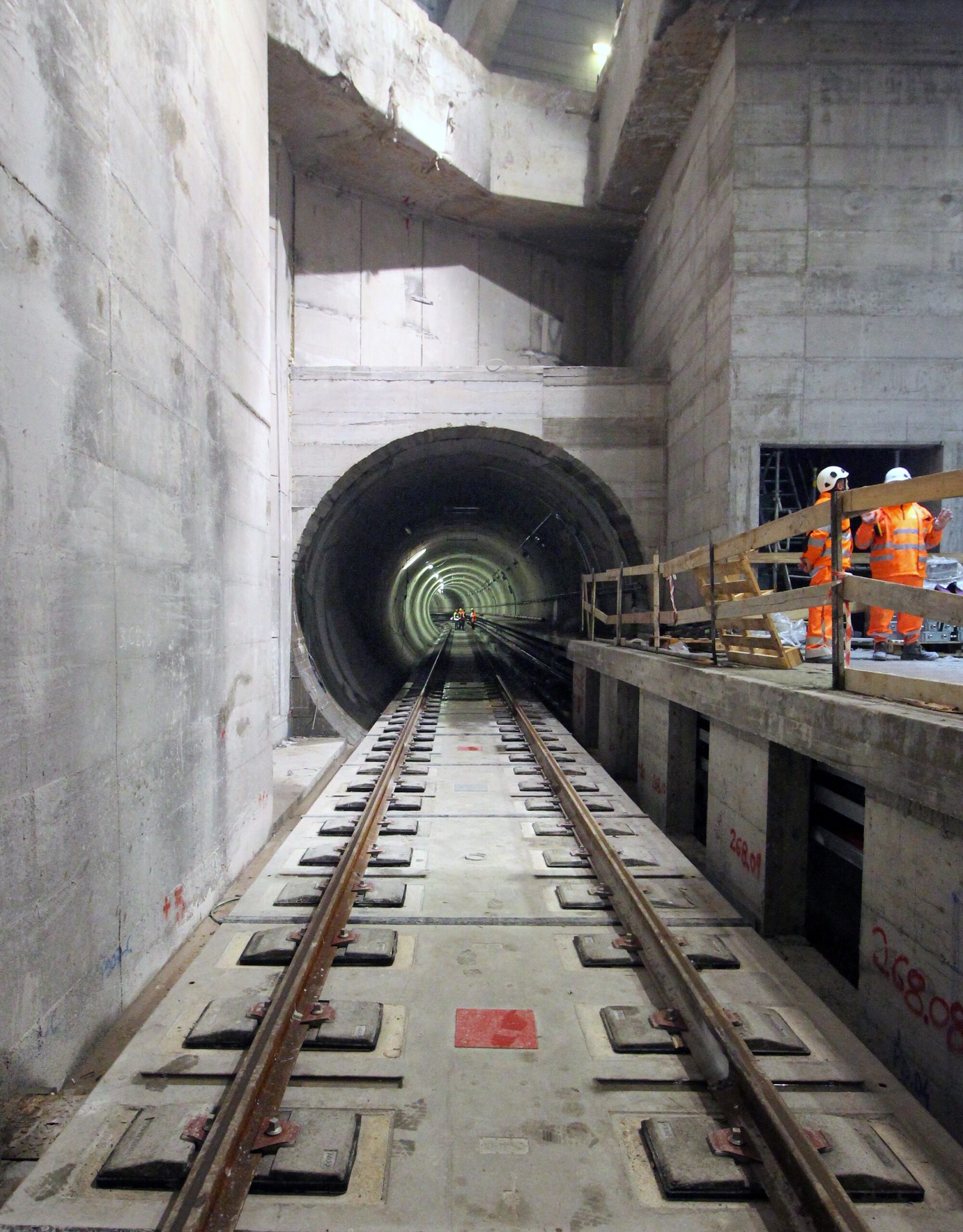
Preparing the Ground for the Future
Within the operational section from Monte Compatri Pantano to San Giovanni, 11 underground stations have been constructed, and an additional 2 stations are currently under construction in the ongoing section.
The underground stations can be classified into 3 types:
- 7 box stations, where the entire structure is contained within the perimeter walls. This type of station was used in all cases where there were no space constraints at street level.
- 3 hammerhead stations, where only the atrium level and the connecting descents to the platforms are contained within the perimeter walls. In this case, the platforms are constructed in a polycentric gallery with traditional widening excavation starting from the TBM tunnel. This station type was used in all cases where, due to street-level constraints, it was essential to reduce the size of open-air excavations.
- 4 stations with a mixed system, where only a part of the structure is contained within the perimeter walls while a portion of the platforms is constructed in a polycentric gallery with traditional widening excavation starting from the TBM tunnel.
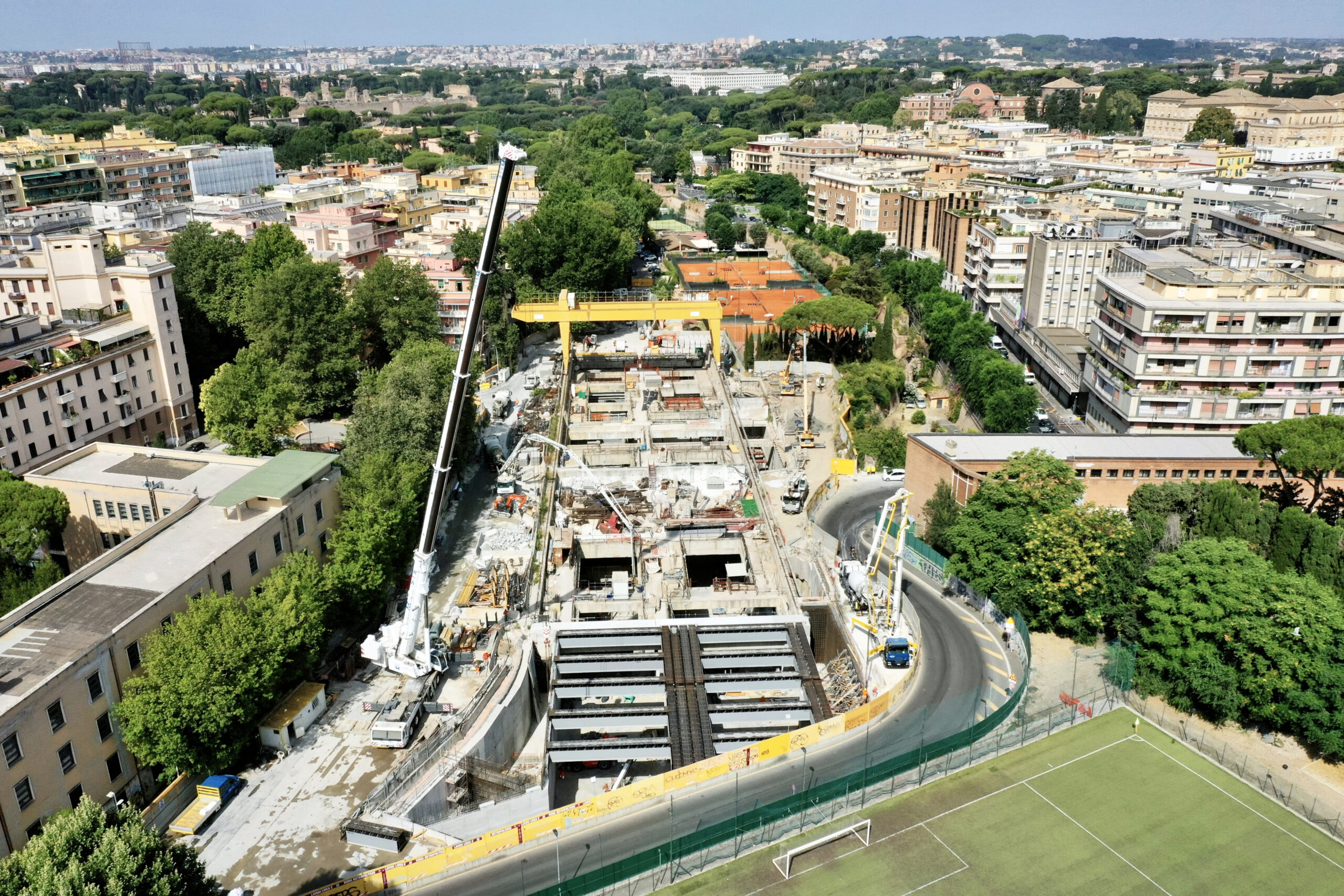
Construction Process
Once the perimeter walls are constructed, the Top-Down excavation begins. This process involves progressively building the ceilings as excavation proceeds, to counteract the perimeter diaphragms and reduce what are known as rear settlements. When the excavation reaches the bottom, if necessary, the platforms are completed through traditional widening excavation starting from the TBM tunnel. In all other cases, perimeter linings are constructed to waterproof and consolidate the structure.
The construction of intermediate section shafts begins with the construction of the containment piles for the excavation of surface premises and the deep shaft connecting to the subway tunnels. Once the bottom of the excavation is reached, the tunnel connecting tunnels to the subway tunnels is excavated using blind hole traditional excavation. In some cases, such as the Malatesta TBM Shaft or the Via Sannio Shaft, due to the construction of an important interchange hub necessary for the railway operation of the line, it was necessary to construct a structure between diaphragms with dimensions comparable to those of an actual station.
Truss Beams
The system of steel truss beams represents a modern construction technology that combines the advantages of prefabrication with the quality of traditional systems (concrete beams, slabs, and pillars), primarily used in cases where there are limits or constraints on excavations, such as those imposed by the presence of significant archaeological structures.
In the context of the construction of Line C, this technology was extensively used for the archaeological excavations at San Giovanni Station, along with the works that make up the section leading from there to Fori Imperiali.
For San Giovanni Station, where the archaeological excavation reached a depth of 20 meters below street level, Metro C S.C.p.A. developed a specific excavation methodology called “Top-Down Archaeological.” This technique involves the downward construction of intermediate floors, placed at least 3 meters from the progressive excavation bottom and required to counteract the pressures on the perimeter diaphragms, using self-supporting prefabricated structures.
This construction system ensures that archaeological excavations can take place simultaneously with the construction of the floors, providing benefits in terms of optimizing construction times and construction site areas.
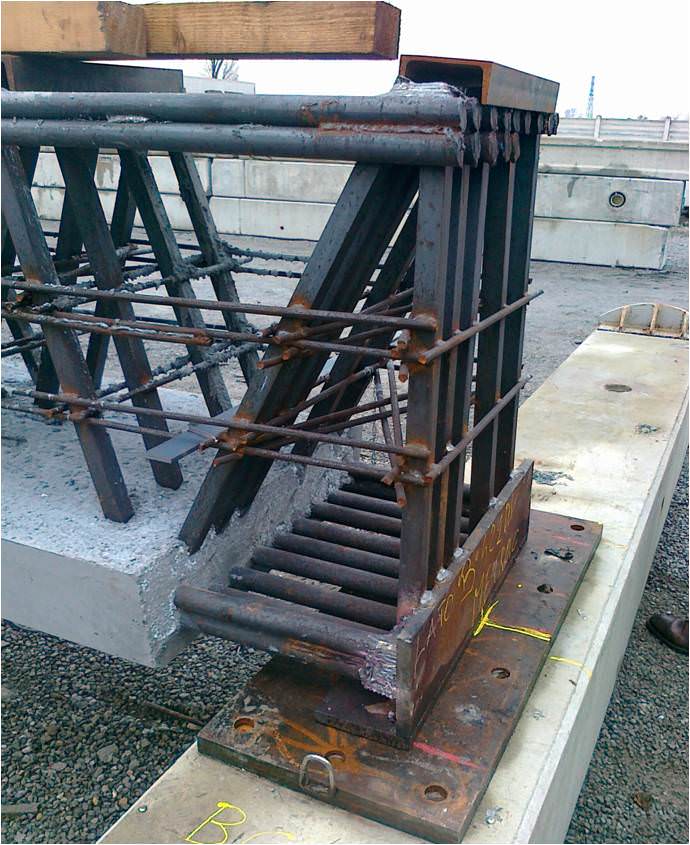
The engineering challenge lies in the complex phase of handling prefabricated structures, which can weigh up to 20 tonnes and have lengths of up to 20 meters. In the case of San Giovanni Station, a special transport and lifting system connected to the floor above the one under construction was designed and implemented. This system allowed for the movement of prefabricated structures along the entire longitudinal development of the station.
For the entire Line C project, the use of approximately 40,000 meters of steel truss beams is anticipated, with a total weight of around 30,000 tonnes. Approximately 10,000 meters of steel truss beams have already been installed in the sections that are in operation and under construction.
The technology of sacrificial diaphragms is a design choice suitable for specific contexts where it is necessary to reduce or eliminate settlements induced by the deformations of perimeter elements (piles or diaphragms) of the excavated structure between shoring walls during excavation.
This technology, which involves the use of non-reinforced diaphragms with a thickness of 120 cm, pushed up to 5 meters beyond the excavation bottom and orthogonal to the perimeter diaphragms, has been adopted beneath the archaeological layer for the Venezia Station project. It is used in a hydrogeological context characterized by soils with poor mechanical characteristics and where important monumental structures are present.
Once the archaeological excavation is completed, the project includes the construction of sacrificial diaphragms that are 46 meters long and will be progressively demolished as the excavation deepens.
For the entire Line C project, including the historic center stations starting from Venezia Station, the construction of approximately 150,000 square meters of sacrificial diaphragms is planned.
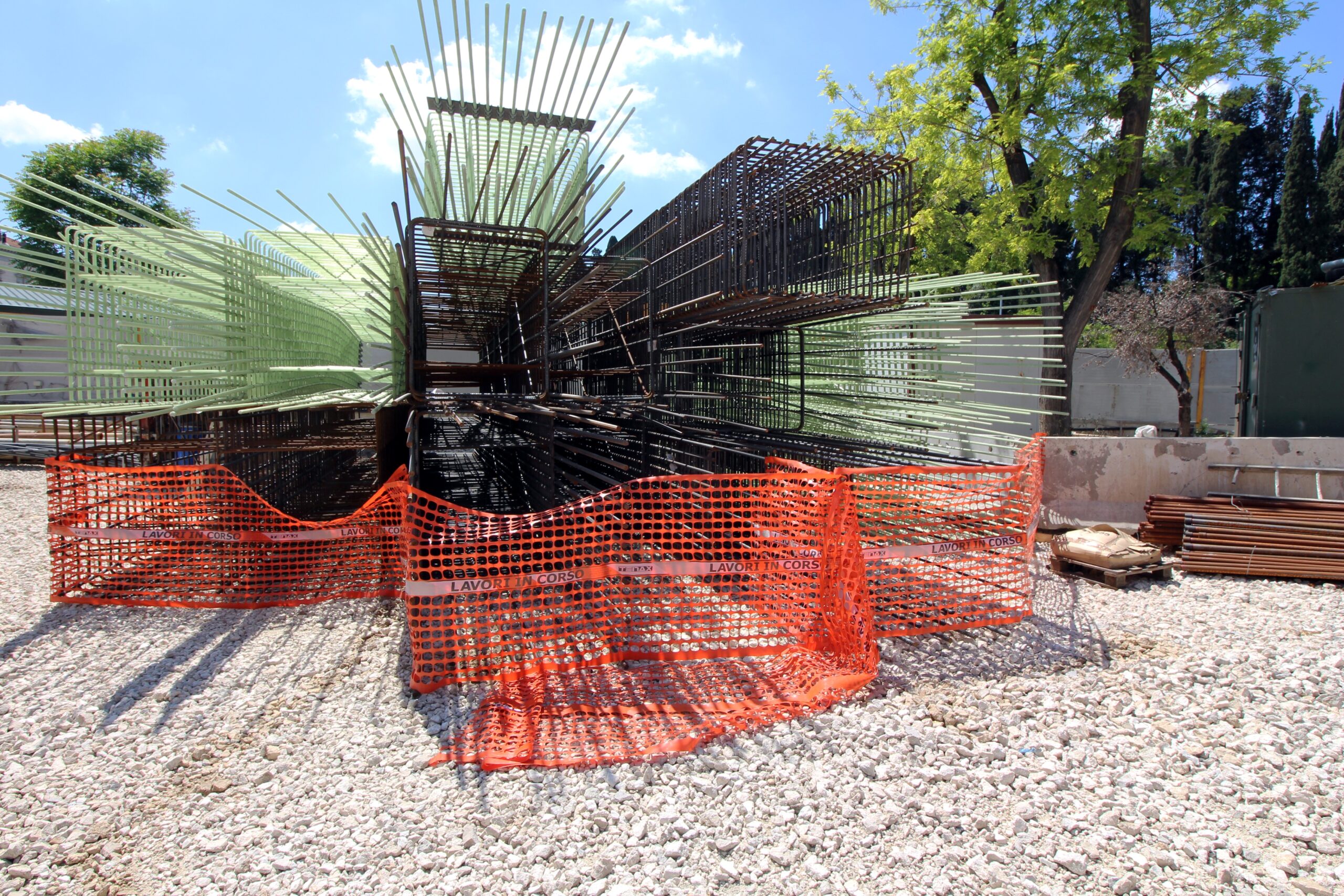
Use of Hydro Milling for Diaphragm Wall Construction
The use of hydro milling for the execution of diaphragm walls ensures both the correct closure of structures (verticality, joints, etc.) and a reduced impact in terms of noise and vibration. Considering the historical-monumental context in which part of Line C is developed and the depths that must be reached to construct the perimeter diaphragm walls of the structures in the relatively impermeable Pliocene clay layer, this construction technology has been widely used for diaphragms with a thickness ranging from 80 cm to 120 cm and lengths of up to approximately 60 meters.
In the context of constructing diaphragm walls, the Venezia Station project within Line C represents a unique challenge worldwide, as it requires the construction of panels with a thickness of 150 cm (compared to the standard 80-120 cm) and a length of 85 meters (compared to the standard 60 meters).
As part of the Line C project, 225,000 square meters of the planned 405,000 square meters of panels have already been executed.
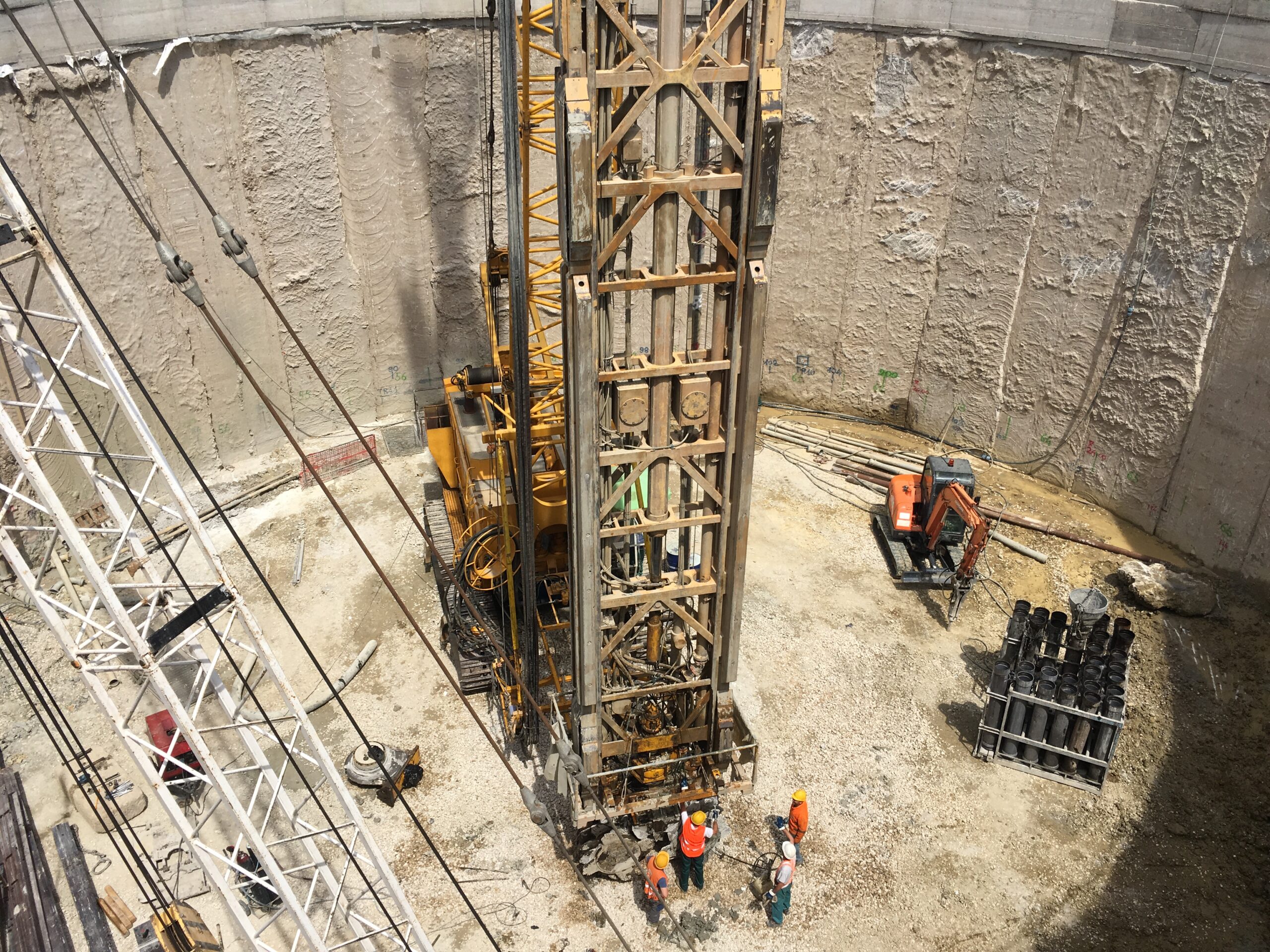
Soil Injection Techniques
Soil injection techniques are methods aimed at improving the mechanical properties (strength and deformability) and hydraulic properties (permeability) of porous soils and fractured or fissured rocks through impregnation and/or filling with cementitious or chemical mixtures.
These treatments involve the pressurized injection – up to a maximum of 16-18 atmospheres – of suitable mixtures through equipped boreholes with valved pipes. The mixtures are fluids (suspensions, solutions, emulsions) with evolving rheological properties, initially suitable for penetration into the porous or fractured medium and subsequently attaining the required characteristics for the treatment’s purposes.
This technology is widely used for soil consolidation in the traditional excavation of underground tunnels below the water table and for creating bottom plugs, also below the water table.
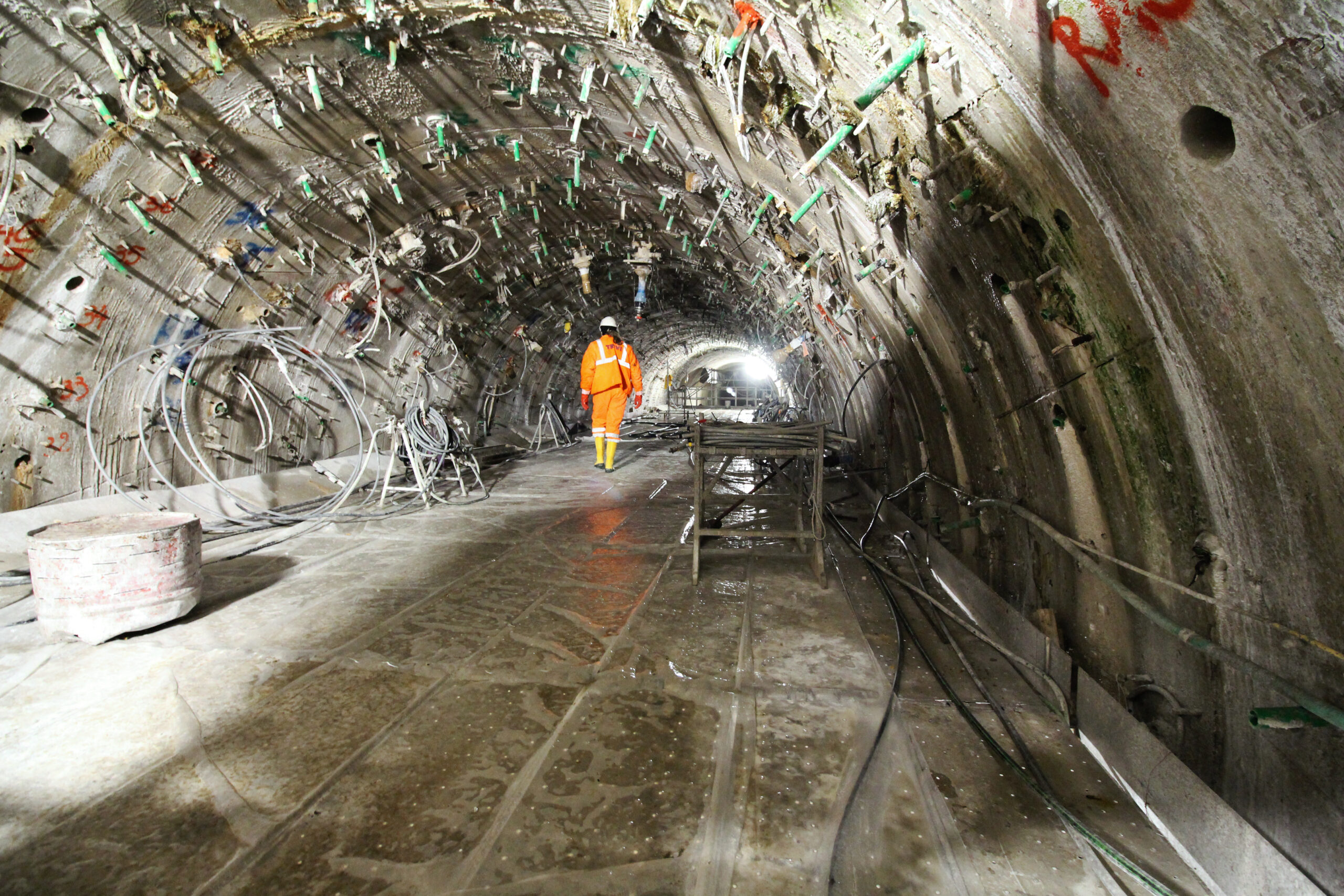